Introduction
Your millwork engineering department is the backbone of your business. It’s not just about producing submittal drawings that mirror the client’s design intent. It’s about detailing the materials, fabrication, and assembly methods you’ll employ. Beyond these primary tasks, they generate detailed cutlists, CNC machine programming, and other pivotal documents to streamline production. Yet, in many millwork organizations, these departments often shoulder additional roles like IT support, material takeoffs, and project management tasks.
Having managed engineering departments ranging from 3 to 85 engineers, I’ve garnered insights and strategies. In this four-part series, I’ll share my blueprint for structuring an engineering department, catering to businesses of all sizes.
To read the first post in the series, visit “How to Structure Your Engineering Department: For Companies with $0M – $5M Revenue.”
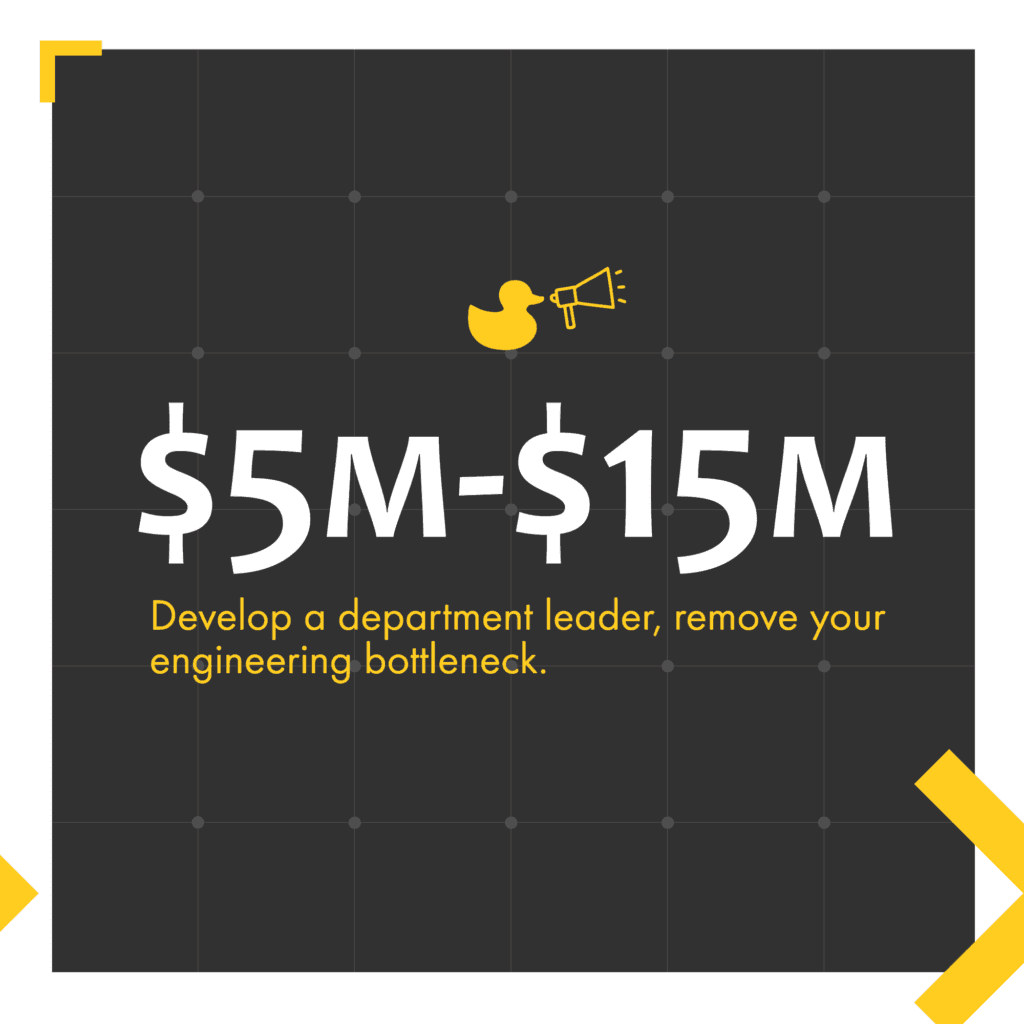
For Companies with $5M – $15M Revenue:
Congratulations, at this stage you have established and scaled the business to a size that is most likely requiring more than just a couple of self-sufficient engineers. Companies with a revenue between $5M and $15M have unique challenges and opportunities, especially in the engineering department. This is the stage where you need to focus on developing a department leader and removing bottlenecks to ensure smooth and efficient operations.
The Bottleneck Dilemma
At this point, your engineering capacity is likely becoming a bottleneck, hindering growth and sales. Managing a highly technical team while pushing them to stay ahead of production can be overwhelming. You might find yourself stuck in a cycle of hand-to-mouth production, constantly waiting for the next project to be completed.
The Common Mistake
A common approach is to promote the most experienced and productive engineer to a leadership position. While this is well-intentioned, it often leads to an overworked engineer and an underperforming manager. The key to success is to transition them from an individual contributor to a manager, focusing on managing the team and their resources effectively.
Developing a Department Leader
To alleviate the bottleneck and drive efficiency, it’s crucial to develop a strong department leader. Their primary functions as an engineering manager now must be:
1. Know Their Capacity:
- Understand the team’s working hours and factor in an efficiency factor, planning for six hours of capacity as a starting point.
- Set daily goals and show the team that they can achieve these goals successfully.
2. Estimate the Demand:
- Avoid relying on budget hours from estimates. Instead, estimate the time required for each task in days, adding a day for review time and potential errors.
3. Schedule Resources:
- Focus on three key dates: the requested date, the planned date, and the actual date.
- Use visual tools like Gantt charts or project management software to provide a comprehensive overview of the team’s workload.
4. Ensure Quality:
- Implement a peer review process to prevent costly mistakes and ensure accuracy in the work.
By investing in developing an engineering leader and focusing on these key areas, you can transform your engineering team from a bottleneck to a defining strength, supporting your business’s needs and growth.
For a deeper dive into these steps, refer to my blog series, “A Simple Blueprint to Successfully Manage a Millwork Design Team.”
Ready to solve the talent shortage and elevate your millwork business? Contact DuckWorks today to discover how our outstaffing services can revolutionize your drafting resources and drive success.