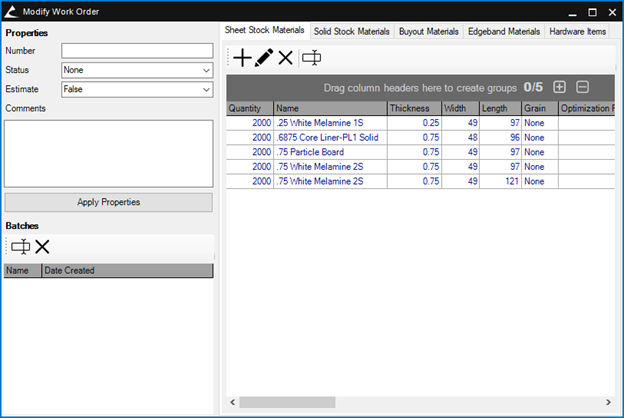
Over the last couple of years, Microvellum has been rolling out updates with some great features that have improved workflows and opened up a lot of new possibilities for users. In this post, I’m going to summarize some of my favorite new features:
1. Modify Work Order Interface
For many years, users have been begging for the ability to edit materials from within a work order, but instead we had been forced to go back and make our changes, and then reprocess the work order. This was a nightmare for efficiency, especially if you were anything like me, and constantly finding mistakes or things that needed to be changed, forcing you to reprocess a work order many times over just to get it all right!
But alas! Microvellum has heard the screeches of engineers the world over, and given us the Modify Work Order Interface. From within any work order, you can now access this from the General menu, and you are presented with a beautiful interface that allows you to edit all of the materials, or even add new materials!
In addition to being able to edit, add or subtract materials, you can edit the properties of the Work Order, including Work Order Number, Status, Estimate, Comments, and even the Batches.
You can read all of the documentation from Microvellum’s open Knowledge Base here: Modify Work Order Interface.
2. Report Groups
Another new feature that greatly increases efficiency is batch printing using Report Groups. This feature is not as new, being made available as of build 15.6.2201, however is is one that I am still extremely pumped about having!
Prior to this feature, when printing reports, users had to individually select each report to send to printer, every time you processed a work order. Even worse, if you needed to save the report to a specific file type instead of just sending to a printer, you would have to open each individual report, and then save from there. This took forever, as each report could take time to open, load and render all of the data, and then the time to make the selections and enter a file name, etc.
Now with Report Groups, this can all be automated, and set to run automatically when processing your work orders. You can even setup multiple report groups and trigger specific reports to only run based on the Processing Stations you have selected, so if you have a CNC report, you can have it run automatically only when you’ve processed to your CNC Processing Stations.
Additional features allow you to specify the output location for the entire Report Group, or by report, as well as to create dynamic file names for the reports.
You can read all of the documentation on this feature from Microvellum’s open Knowledge Base here: Report Groups (Overview)
3. Parts List Review
This feature is a hidden gem that I accidentally stumbled upon recently, but it is phenomenal.
Previously, to get a consolidated list of parts from your products to verify materials, edgebanding, part sizes, etc. you would have to create a work order, and process to get the parts list. This was a very inefficient and time consuming way to find out something is wrong with your products or parts!
Now, there is a feature in the Product List that you can use to select multiple products, and then right click, and select Parts List Review, and you get get a full consolidated list of parts, that you can sort, group, and filter to verify everything in those products as it will be when processing.
That’s my list for now, I hope you learned something new from it. If you’ve got other new features you think should have been on this list, post them below in the comments!