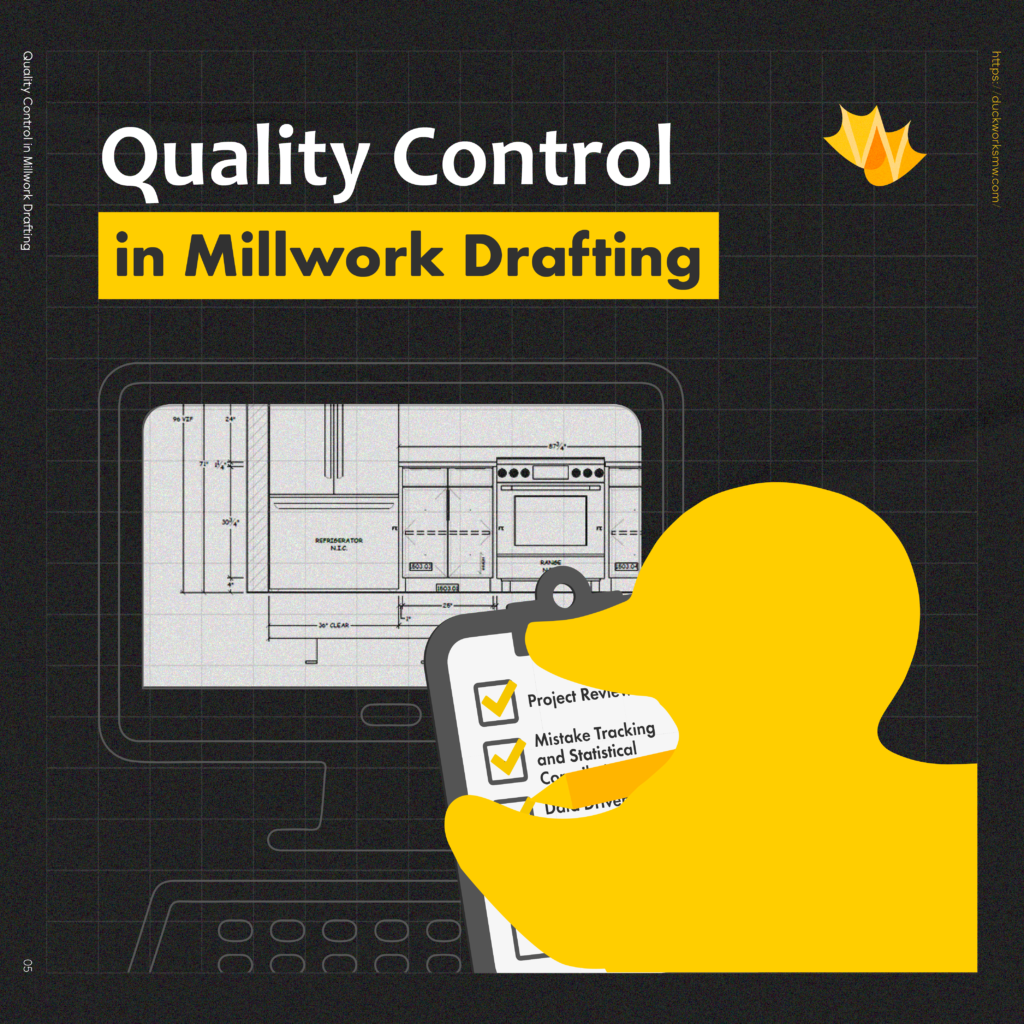
Quality control in millwork drafting and design is essential to ensure that final products meet design specifications, safety standards and functional requirements. This process involves several key components that help maintain a high level of quality during the design and manufacturing phases.
Importance of Quality Control
- Accuracy: Shop drawings should represent the customer’s proposed design as accurately as possible. By implementing a quality process, dimensions, materials and consistency can be verified to reduce potential errors during fabrication and subsequent installation of the products.
- Cost control: Identifying inconsistencies at the drawing stage can prevent errors that can result in wasted materials and even man-hours. This step allows our customers to maintain their planned budgets and work schedules.
- Standards Compliance: The industry has several standards and specifications that must be followed. QC processes help ensure that these standards are met and that specifications are present on drawings.
DuckWorks Quality Control Process
At DuckWorks, we have developed a quality control process to minimize errors in attention to detail. Through analysis this also provides us with valuable statistical information that allows us to make changes and improvements in the drawing process itself and complements the ongoing development of the skills and experience of the drafter. We have a specific QC team that review your drawings at different stages of the project.
Here you can find a summary of the key steps involved in our QC process, each designed to ensure that we consistently meet client expectations.
- Project Review:
The goal of the first step is to identify drawing inconsistencies and generate markups for corrections, ensuring the project meets quality standards. To achieve this, we use a preliminary checklist to pinpoint discrepancies during the Bluebeam session, comparing the drawings against the client’s established quality standards:
We start by carefully reviewing the project to find any drawing mistakes, focusing on client standards, and creating notes for the necessary changes. This review includes a clear list of project aspects that need to be checked, ensuring the project meets quality standards and client expectations. The quality control review list consists of the following points:
Figure 1: Quality Control Checklist

Source: Duckworks Millwork Solutions Quality Control Management
This feedback helps the team correct any issues, improving the overall consistency of the drawings.
- Mistake Tracking and Statistical Compilation
Monitor and document mistakes identified during the review process, conducting a detailed count and statistical analysis to establish metrics for each project.
Figure 2. Pareto Chart: Distribution of Mistakes in Quality Control (80/20 Rule)
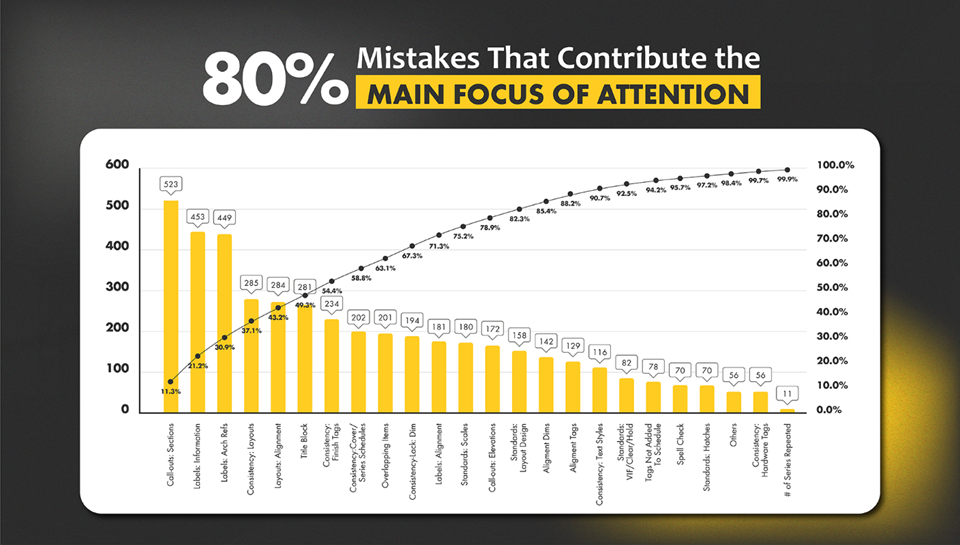
Source: Duckworks Millwork Solutions Quality Control Process Data
This step is to systematically monitor, quantify, and document errors identified during the review process. This includes conducting a thorough count of mistakes across all drawings and documenting observations. After that a statistical analysis is performed to derive metrics for each drawing, providing valuable insights into error patterns, project status, and KPIs for decision-making and targeted improvements in drawing and quality control procedures.
- Data-Driven Report Generation:
We prepare weekly reports to identify areas where we can enhance efficiency and quality in our work. These reports include statistical data that clearly show the percentage of quality improvement across all projects reviewed each week, highlighting trends in mistakes compared to the previous week. This allows us to recognize specific types of errors that may need more attention. The final report also includes targeted recommendations based on our observations and notes, ensuring that the team can focus on areas for improvement or celebrate excellent performance when it’s deserved. This structured approach helps us continually refine our processes and supports the growth of our drafting team.
Figure 3. Quality Control Report per Project
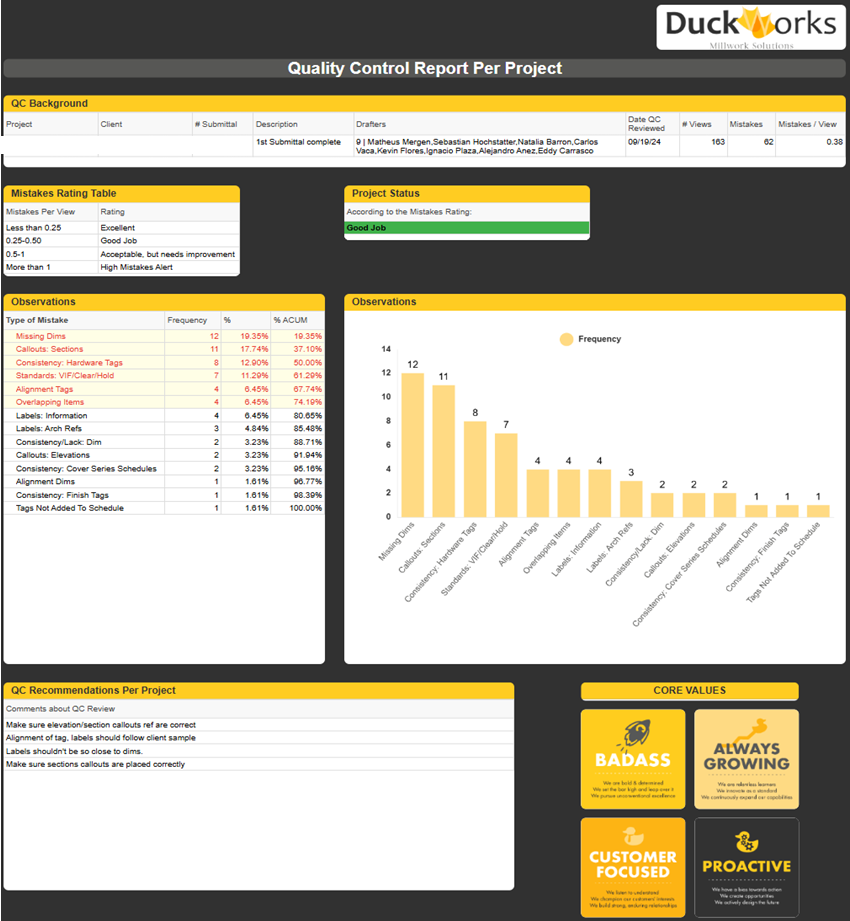
Source: Duckworks Millwork Solutions Quality Control Dashboards
- Report Dissemination
In the next step of our QC process, we share the weekly QC report with Team Leaders and Supervisors for each project. We distribute the reports through Microsoft Teams, ensuring they reach the appropriate channels for every project.
This streamlined communication allows all relevant team members to review the findings and recommendations promptly. By making the report easily accessible, we encourage collaboration and discussion around the insights, encouraging a culture of continuous improvement and accountability within the team. This step ensures that everyone is aligned and informed, enabling us to take effective action based on the report’s findings.
Figure 4. Quality Control Report per Project

Source: Duckworks Millwork Solutions Quality Control Dashboards
- Feedback Meetings
We hold feedback meetings with the project team where we analyze the recommendations from the report and discuss the inconsistencies identified in the QC review. This step allows team members to reflect on the quality observations specific to their projects and helps the QC team understand the causes of the issues and challenges they encountered while drawing. This exchange of ideas not only fosters a sense of ownership but also helps us collectively identify practical solutions and improvements for future work.
Implementing solid quality control measures in millwork drafting is essential for delivering great results in millwork projects. By prioritizing accuracy, clear communication, and proper documentation, we can ensure we meet our client’s expectations and stay in line with industry standards. This approach not only helps build trust with clients but also supports successful project outcomes.


Alejandra Lopez
Chief of Staff
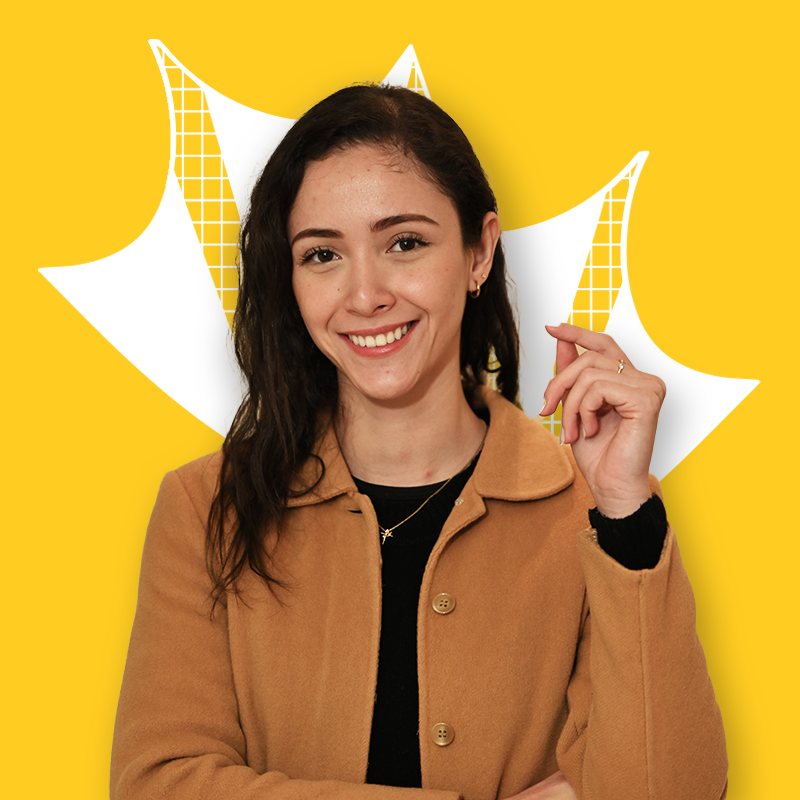
Fernanda Salmon
Quality Control